Экструдер для производства пеллет — делаем своими руками
Здравствуйте уважаемые читатели и подписчики блога, на связи с вами Андрей Ноак! Сегодня я расскажу вам как сделать экструдер для производства пеллет в домашних условиях.
Введение
Как говорится каждому свое. Кто то делает десятки тонн пеллет в сутки на большом современном производстве, а кому то нужен обычный небольшой гранулятор для переработки соломы, опилок или других отходов. Вот такой небольшой гранулятор мы сегодня и рассмотрим.
Сразу хочется сказать, перед прессом должно быть предусмотрено сито или хотя бы сетка и магнит, которые будут отделять крупную фракцию от мелкой и отсортировывать металлические примеси.
Бывают случаи попадания в гранулятор гаек, ключей, металлических предметов, при переработке кормов могут попадаться камешки и галька. Это сразу ведет к выходу из строя каких то частей экструдера, а может даже и к полному его выходу из строя. Поэтому дешевле перестраховаться и снизить вероятность попадания того что не должно.
Гранулятор или экструдер?
Как вы уже поняли гранулятор и экструдер хоть и делают гранулы, но по своему строению отличаются и прежде чем делать какой то станок нужно для себя понять какой конкретно станок вам нужен.
Состоит экструдер или как его еще называют шнековый пресс из:
- Шнека;
- Матрицы;
- Корпуса;
- Мотор редуктора.
Такой пресс как правило применяется, как я уже говорил, в домашних условиях, для переработки десятков килограмм отходов. К примеру загранулировав сухие опилки, можно их подмешивать к углю и снизить потребление покупного угля. А можно гранулировать солому и потом гранулы делать подсыпкой к животным. Вариантов использования много и описывать в данной статье я их все не буду.
Давайте же посмотрим отличия шнекового пресса от обычного гранулятора:
- Изготовление шнекового, в небольшой мастерской будет гораздо проще чем гранулятора;
- Более простое строение — более надежная конструкция;
- Производительность такого станочка будет гораздо ниже, и если грануляторы идут от 300 кг/час, то шнековые будут до 300 кг/час.
Можно конечно сделать и с большей производительностью, но это будет очень большая машинка;
- Гораздо более простая матрица, которую можно сделать проще на обычном токарном станке.
Инструменты
Давайте посмотрим что нам понадобиться в процессе изготовления:
- Сварочный аппарат;
- Токарный станок;
- Сверлильный станок, дрель не рекомендуется (отверстия кривые выходят;
- Болванка металлическая под матрицу;
- Трубы для корпуса пресса;
- Прут металлический 10 мм;
- Подшипники — 2 шт., выбираются в зависимости от диаметра посадочного отверстия;
- Мотор редуктор.
Изготовление
Подготовка, составление чертежей
Перед изготовлением нужно для себя определить какие размеры будут у вашего станка, каким диаметром шнек и какая матрица. Я не буду сейчас давать какие то конкретные цифры, так как в каждом случае это индивидуально. У кого то подшипники есть маленько другого размера, зачем ему покупать то что я говорю?
Итак вам нужно будет расчертить все размеры на бумаге.
Но сделать это лучше только после прочтения данной статьи, чтобы чертить сразу с учетом всех нюансов.
Шнек
Первое, с чего начинается изготовление это шнек. Для его производства не нужно каких то супер станков, будет достаточно того о чем я писал ранее.
Начинается изготовление с выбора вала, затем проточка посадочных под подшипники и наварка прута. Чем больше шаг, тем будет меньше давление на матрицу, но больше производительность. Чем же меньше шаг, тем меньше производительность пресса, но больше давление.
После наварки прута, обрабатываем его болгаркой. Наш шнек готов! Чтобы все было более понятно вот вам пошаговое видео:
Матрица
Для матрицы подойдет обычная сталь 45, на видео ниже ее изготавливают из нержавейки. Нержавейка будет дольше ходить, но на такой производительности вопрос износа матрицы стоит не столь остро. Если к примеру завод делает 20 тыс тон пеллет и у него выходит из строя матрица.
Небольшая матрица из железа вам отслужит 3 — 5 лет без проблем, его проще найти чем нержавейку.
Наружный диаметр матрицы должен быть равен наружному диаметру шнека.
Разметка фильер матрицы может производиться как на видео ниже, прямо на токарном станке, так и накладкой бумажного чертежа с отверстиями на заготовку и затем накернение и рассверливаете, в общем в этой статье имеется подробная инструкция. На видео ниже показан первый способ изготовления.
Не забываем — последний этап, это зенковка матрицы!Корпус
Для изготовления гильзы нам понадобиться труба. Можно не делать как на видео сложный корпус состоящий из трех частей. Достаточно взять одну трубу в качестве главного корпуса и вставить в нее сменную гильзу. Гильза приваривается (правильнее прихватывается) к главной трубе. Использование гильзы как показано на видео повышает ресурс работы станка.
Нужно добиться такого эффекта, чтобы гильза внутри не прокручивалась с шнеком.
Не забываем про изготовление загрузочного отверстия. Его также не нужно изготовить из куска трубы меньшего диаметра.
По торцам основного корпуса устанавливаются фланцы. Хотя тут уже смотрим видео, на нем все подробно показано.
При установке подшипников, я бы рекомендовал конусные роликовые. Они более устойчивы к нагрузкам.
Мои книги и услуги
Совсем недавно у меня вышла книжечка. Отличное руководство для тех кто хочет организовать не просто домашний пресс, а большое и крупное производство гранул. В книге даются фишки по технологии, которые я наработал сам, методом проб и ошибок. Более подробно о книге можно узнать в разделе «МОИ КНИГИ».
Кроме книги могу предложить свои услуги в подборе под вас конкретного оборудования, могу проконсультировать как и что лучше сделать чтобы избежать каких то проблем уже при эксплуатации оборудования. Для того чтобы связаться со мной, нужно обратиться в поддержку (см. верхнее меню).
Удачи и до новых встреч, с вами был Андрей Ноак!
Как улучшить кормоэкструдер — модернизация своими руками | Своими руками
Почти все фермеры-животноводы рано или поздно сталкиваются с проблемами, связанными с приобретением качественного комбикорма. У кого-то нет поблизости завода, производящего нужную продукцию, кому-то не подходит ее качество или цена…
Пришло время, и в нашем шиншилловодческом хозяйстве вопрос доступного корма тоже встал во главу угла. А не проще ли делать его самостоятельно, своими руками, задумались мы? И вскоре приобрели кормоэкструдер КЭШ-1. Однако после покупки быстро выяснилось, что агрегат требует серьезной доработки.
Наш кормоэкструдер с трехфазным мотором еле-еле справлялся с нагрузкой. Во время работы у прибора часто срабатывала защита от перегрева и перегрузки, после чего запустить его без полной разборки прессующего узла было уже невозможно.
Дозирующее устройство издавало такой звук, словно мы находились в кузнечном цехе. Накопительная воронка постоянно забивалась, и приходилось пробивать ее с помощью палки. Дозирующий клапан наотрез отказывался адекватно отмерять помол, разбрасывая его во все стороны. Через два месяца шнеки полностью сносились. Примерно в это же время обломился у основания вал шнека.
Переписка с заводом ни к чему не привела. Но наша задача состояла не в том, чтобы судиться и наказать производителя некачественной продукции. Мы хотели делать собственные корма. Поэтому постарались модернизировать кормоэкструдер и все же заставить его трудиться на наше благо.
В Интернете отыскалось немало публикаций от владельцев КЭШ-1, столкнувшихся в процессе эксплуатации агрегата со схожими проблемами. Поэтому надеемся, что наш опыт переделки кормоэкструдера будет полезен многим.
Читайте также: Кормушка для домашней птицы своими руками
Делаем кормоэкструдер лучше и удобнее своими руками
1. Первое, с чего мы начали, заменили установленный мотор 2,2 кВт на мотор 4 кВт российского производства. Замена оказалась не такой легкой задачей: пришлось переваривать площадку крепления мотора и менять механизм натяжки приводных ремней. Но в итоге все же удалось поставить в КЭШИ новое «сердце».
Первый же запуск показал, что мы на правильном пути. Перегревы и самоотключения исчезли. Старт прибора после остановок стал возможен без предварительной разборки и чистки пресс-узла.
2.Затем мы развернули весь прессующий механизм в противоположную сторону. Теперь выброс готового сырья происходит за пределы корпуса экструдера в специально приспособленный пластиковый ящик. Для этой переделки пришлось пересверливать крепежные отверстия пресс-узла к корпусу и переключать двигатель для вращения в другую сторону.
3. Вскоре руки дошли и до всего узла дозации. Мы изготовили дозатор с шнековой бесшумной подачей сырья. В качестве подающего шнека использовали винтовое сверло по дереву длиной 600 мм и диаметром 30 мм.
В качестве привода взяли моторчик с планетарным редуктором от шуруповерта. Дополнительно в цепь питания моторчика включили автоматические биметаллические автомобильные предохранители на 25 А. Для стыковки редуктора со спиральным сверлом потребовалась специальная насадка для шуруповерта и шестигранная головка на 11 мм. В результате нам удалось повысить производительность экструдера с заявленных 20-30 кг в час, до 60-70 кг в час, то есть больше чем в два раза.
4. Загрузочный бункер мы оснастили ворошителем
Ворошитель представляет собой металлический вал с двумя лопатами, закрепленный по краям в подшипники. Вал располагается параллельно шнеку, при вращении лопатки почти прикасаются к шнеку и постоянно подкидывают на спираль свежую дозу корма. А шнек, в свою очередь, доставляет сырье в приемную воронку экструдера. В качестве редуктора ворошителя использовали мотор-редуктор на 12 В от автомобильного стеклоочистителя (ГАЗ – ВАЗ 2108).
Моторчик подключили через автоматический предохранитель и реле паузы. Постоянного ворошения не требуется, а пауза не дает мотору перегреваться. В качестве кнопок включения подающего шнека и ворошителя использовали выключатели аварийной сигнализации от ВАЗ-2108. Эти выключатели имеют встроенную светодиодную подсветку, а главное – их контакты хорошо защищены от попадания пыли.
5. На панель управления добавили вольтметр и амперметр, благодаря которым можно контролировать нагрузку на основной электродвигатель.
Фильеры, валы и шнеки впоследствии были заменены на новые, изготовленные на заказ на металлообрабатывающем заводе.
С помощью усовершенствованного экструдера мы производим корм для подсосного молодняка и кормящих самок, а также делаем витаминные вкусняшки – фруктовые «колбаски», похожие на кукурузные палочки, которые с огромным удовольствием поедаются всеми шиншиллами.
Ссылка по теме: Автоматическая кормушка для кур своими руками
Модернизация кормоэкструдера своими руками- фото
© Автор: М.БАКИЕВ Московская обл.
ИНСТРУМЕНТ ДЛЯ МАСТЕРОВ И МАСТЕРИЦ, И ТОВАРЫ ДЛЯ ДОМА ОЧЕНЬ ДЕШЕВО. БЕСПЛАТНАЯ ДОСТАВКА. ЕСТЬ ОТЗЫВЫ.
Ниже другие записи по теме «Как сделать своими руками — домохозяину!»
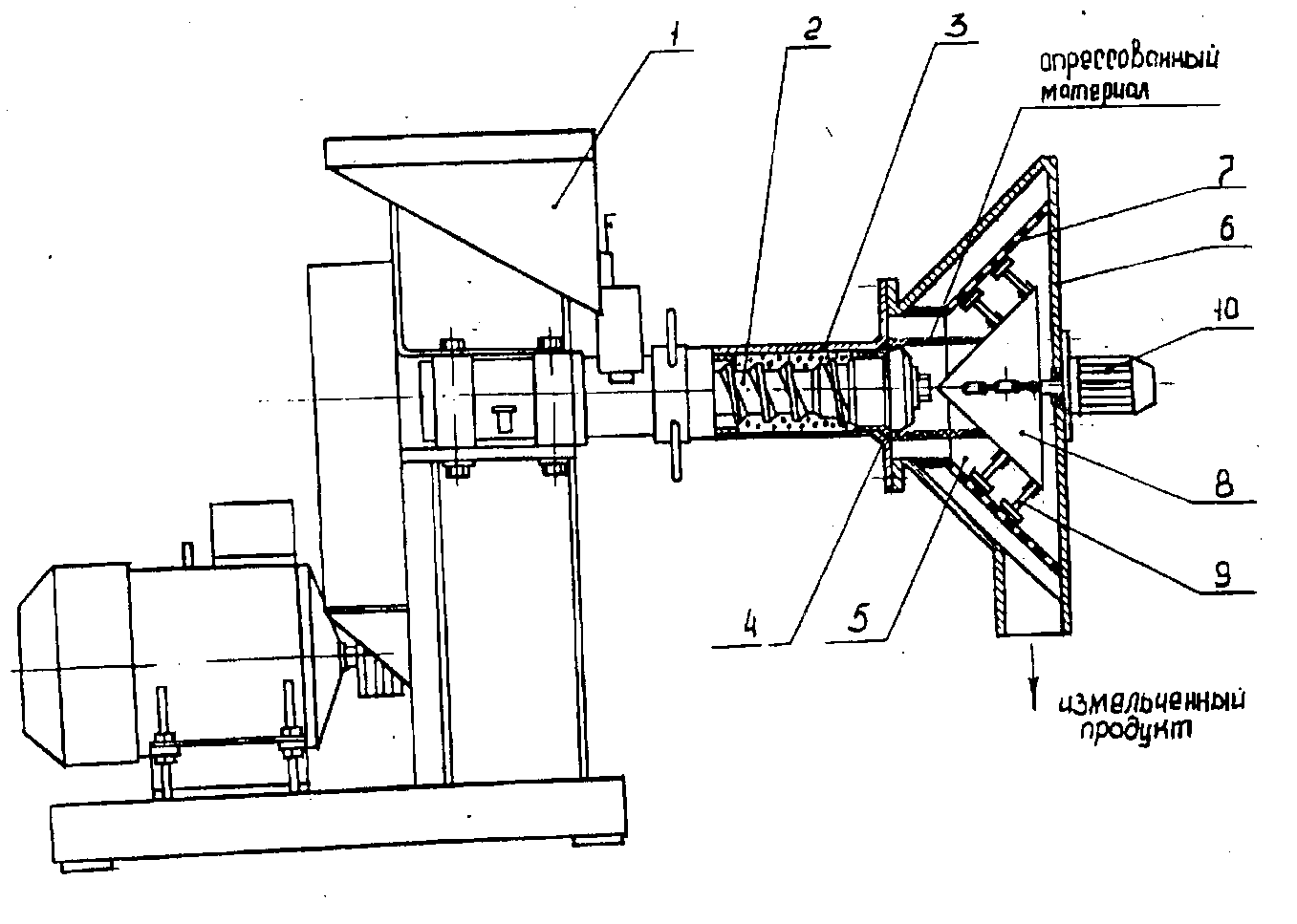
Подпишитесь на обновления в наших группах и поделитесь.
Будем друзьями!
Экструдер из мясорубки для производства филамента
brtvЗагрузка
20.07.2020
13980
Подпишитесь на автора
Подпишитесь на автора, если вам нравятся его публикации. Тогда вы будете получать уведомления о его новых постах.
Отписаться от уведомлений вы всегда сможете в профиле автора.
58
Статья относится к принтерам:
Anet A8Первый тест экструдера из мясорубки собранного в домашних условиях. Думаю провести тесты с многими видами пластика и перерабатывать такие типы пластиков, как: ABS HIPS PETG PLA PVA и другие
ссылка на видео: https://www.youtube.com/watch?v=n5a2KKbK35A
Подпишитесь на автора
Подпишитесь на автора, если вам нравятся его публикации. Тогда вы
будете
получать уведомления о его новых постах.
Отписаться от уведомлений вы всегда сможете в профиле автора.
ПодписатьсяЕще больше интересных постов
dallas9Загрузка
06.11.2020
4046
21Подпишитесь на автора
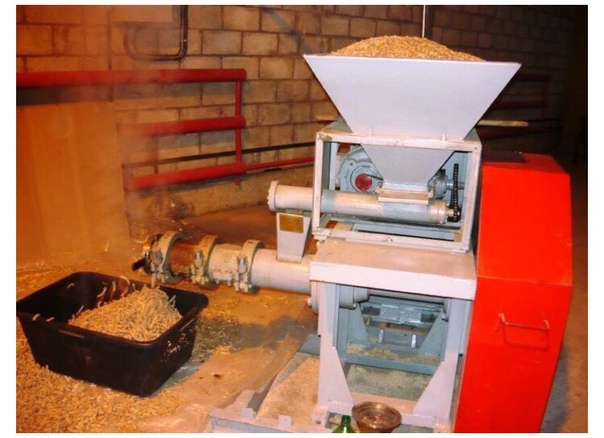
Отписаться от уведомлений вы всегда сможете в профиле автора.
Подписаться PVP == поливинилпирролидонМного было материалов про такие клеи, покупные и самодельные, разные рецепты на разный вкус, но все они бы…
Читать дальше i3DЗагрузка
30.10.2020
777
2Подпишитесь на автора
Подпишитесь на автора, если вам нравятся его публикации. Тогда вы
будете
получать уведомления о его новых постах.
Отписаться от уведомлений вы всегда сможете в профиле автора.
Подписаться Друзья и коллеги!Приглашаем вас принять участие в конференции «3D-решения для ремонта и печати изделий из металла»….
Читать дальше РоманЗагрузка
28.03.2016
57456
209Подпишитесь на автора
Подпишитесь на автора, если вам нравятся его публикации. Тогда вы
будете
получать уведомления о его новых постах.
Отписаться от уведомлений вы всегда сможете в профиле автора.
Подписаться Обработка парами ацетона.Решил написать пост, тем самым отвечая на часто задаваемые вопросы клиентов, которые приобретали у меня…
Читать дальшеЭкструдер для переработки пластика своими руками
Всем привет !Нужны советы по созданию экструдера, для переработки пластика
Печатаю много такого
(отечественная техника тоже есть не волнуйтесь)Остается брак и поддержки , хотелось бы и их пустить в дело !
Начну с того что имею на данный момент:
— Доступа к сварочному аппарату у меня нет , использую то что можно купить в магазине и на Алиэкспрес
1) кусок трубы с резьбой + нагревательный элемент + заглушка (в заглушке резьба под сопло от 3д принтера с отверстием 1,7 мм) для универсальности процесса
2) Станина и крепление + латунный тройник 3) Сверло с доп заглушкой и отверстием под сверло Из электроникиНагреватель (в комплекте 2 , но 1 я угробил )
http://ali. pub/3ees1i
Заказал еще такой вариант
http://ali.pub/3ees8p
Мозги нагрева + термопара + реле
http://ali.pub/3eesd6
***********************— В ходе экспериментов оказалось что 1 нагревательный элемент мало , 2 много … Во общем минимум 2 , иначе провернуть шнек (сверло ) становиться тяжело во всех смыслах.
выход пластика нормальный, шнек крутил руками, качество пластика … ну неплохое , ожидал хрупкость и ломкость , но получилось что то похожее на PLA , хотя перерабатывал ABS.
************
А теперь к главному
По задумке вращать шнек должен двигатель (от старого патифона) но силы ему явно не хватает
с плавностью регулировки все не очень..она как бы есть и как бы нет … (питание 220в , регулятор оборотов ниже) Фото двигателя прогресса : + перегрев шнека диформирует АБС колесо по которому идет ремневая передача (хотя от этой идеи я пожалуй откажусь , все очень не надежно)******************
В общем Вопросы следующие :
Стоит ли использовать шаговый двигатель? и какой ? (вместо того что я вам показал)
Как и чем его питать и регулировать обороты ?
В электронике я почти 0 , нужны готовые решения (типо с алика )
Буду рад если поделитесь опытом и идеями !
( Об узлах контроля и протяжки прутка пока не будем, не хочу загадывать далеко )
(если что моя группа https://vk. com/public_model_hends)
Еще несколько фото
Как сделать экструдер для переплавки пластмассы из пистолета для герметика
Многие виды пластика являются полезным сырьем для вторичной переработки. Расплавив их в пластичную массу можно изготовить самодельный филамент для 3D принтера или фигурки, сувениры и прочие поделки. Рассмотрим, как можно сделать ручной компактный экструдер для переработки пластика.Материалы:
- пистолет для герметиков;
- стальная трубка;
- асбестовый шнур;
- нихромовая нить;
- провод с вилкой;
- механический терморегулятор от электродуховки;
- пластиковая бутылка от моющего средства;
- скотч;
- песок;
- гипсовая штукатурка.
Изготовление экструдера
На отрезок стальной трубы равной по длине тубу для герметиков наматывается асбестовый шнур. Важно, чтобы торец трубы был заварен и имел небольшое центральное отверстие.
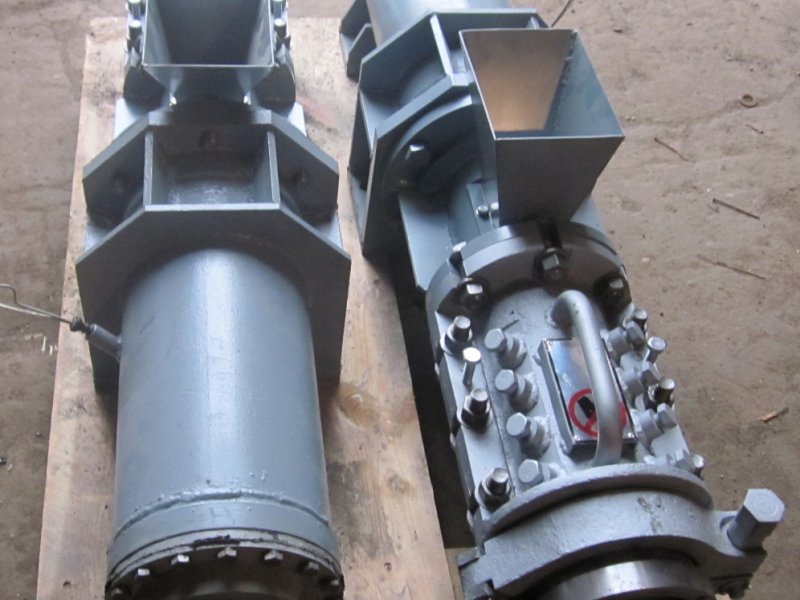
Поверх асбеста наматывается нихромовая нить. Ее можно получить из выровненной спирали от электроплиты.
Затем спираль закрывается новой обмоткой из асбестового шнура.
На пистолет от герметиков закрепляется механический терморегулятор от духовки. Его нужно закрепить так, чтобы ручка регулировки располагалась с тыльной стороны пистолета.
Из пластиковой бутылки от моющего средства изготавливается форма для литья в виде трубы. Для этого у нее срезается дно и горловина, после чего она распускается вдоль.
С одной стороны заготовка подгибается, и на изгибе вырезаются зазубрины. Полученный лист наматывается на любую трубку диаметром около 5 см. Затем заготовка закрепляется скотчем. Зазубрины при этом формируют ее дно. Сбоку полученной формы нужно сделать небольшое отверстие равное диаметру термодатчика. В него требуется вставить трубку из свернутого листового пластика.
Затем в форму из бутылки помещается стальная трубка с обмоткой из нихромовой нити и асбестового шнура.
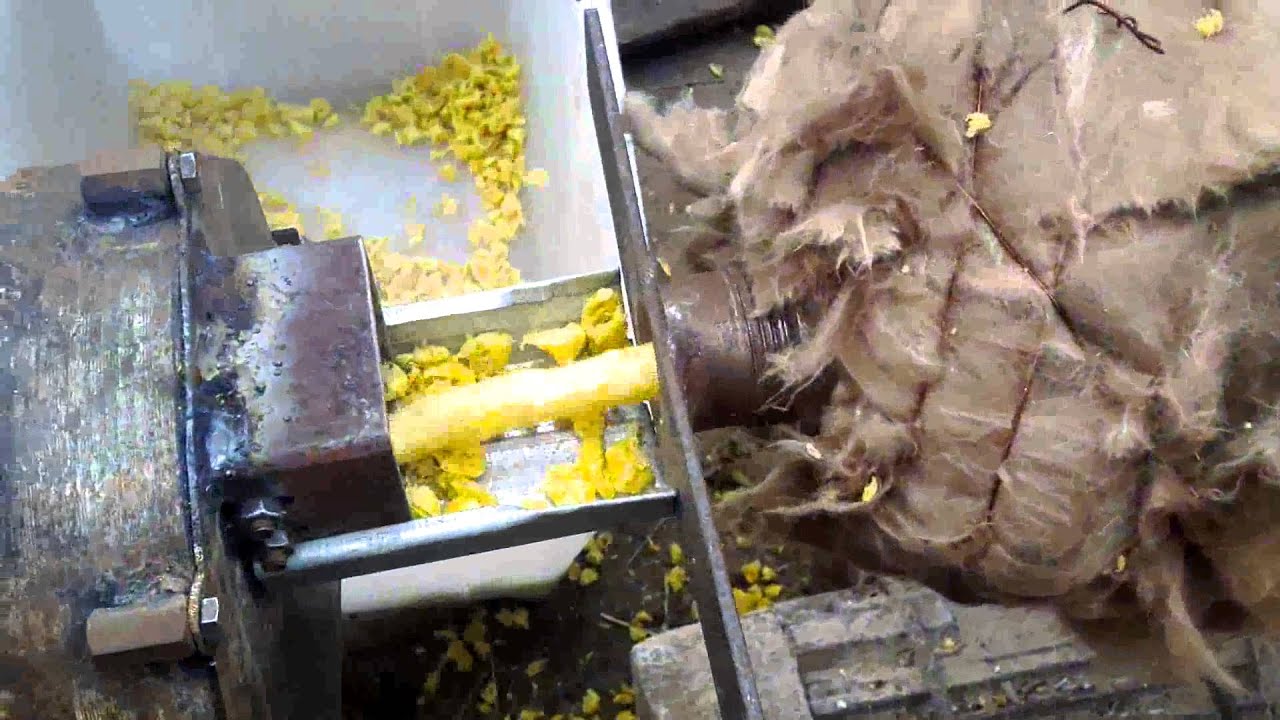
Далее в пустое пространство между пластиковой оболочкой и стальной сердцевиной заливается термостойкий раствор, приготовленный из песка и гипсовой штукатурки.
После застывания раствора верхняя трубка из обрезанной бутылки удаляется.
В боковое отверстие свободное от раствора устанавливается термодатчик, который закрепляется хомутом. Концы нихромовой нити подключаются к электрокабелю с вилкой. Внутрь стальной трубы засыпается пластиковая крошка. Это может быть HDPE пластик из мелко нарезанных крышечек от ПЭТ бутылок, или ABS пластик, который можно получить из корпусов старой бытовой техники.
Далее заправленная пластиком труба устанавливается в пистолет для герметиков. В нее запускается шток пистолета с тарелкой. Если тарелка окажется большой, то ее нужно предварительно обточить. Теперь включив вилку в розетку и отрегулировав температуру можно разогреть массу.

Полученный экструдер можно использовать по-разному. Если поставить на конец трубы тонкий носик, то удастся получить филамент для 3D принтера. Также горячую массу возможно выдавливать в различные формы, делая фигурки, ручки для мебели, детали для механизмов и т.д.
Смотрите видео
Особенности экструдера, сделанного своими руками
Экструзия является популярным методом получения полуфабрикатов или товаров, произведенных из полимеров любой длины, поэтому сделанный экструдер своими руками в некоторых случаях позволит сэкономить вам деньги. Данный процесс используют в пищевой промышленности или в производстве комбикорма. Процесс происходит так: расплав полимера выдавливается при помощи головки экструдера в формующую головку с необходимым профилем. Данный способ производства наряду с литьем пластмассовых материалов под давлением сейчас один из наиболее популярных. Практически все полимеры могут подвергаться экструзии: термопласты, эластомеры и другие материалы.
Схема работы сварочного экструдера.
Технология экструдера применяется уже больше шестидесяти лет. За этот длительный период появилось достаточно большое количество машин, которые изготовлены специально для использования данной технологии. Если детально рассмотреть экструдер, то можно понять, что это такое. Процесс экструзии является достаточно сложным, основан он на физических и химических законах. Процесс проходит непосредственно под влиянием механических действий при воздействии высоких температур и наличии влаги. Из-за того, что механическая энергия обращается в тепло, которое выделяется вследствие внутреннего трения, при обработке материал подвергается нагреву.
При обработке экструзионной техникой есть несколько сменных характеристик: состав предоставляемого сырья, процент его влажности и природа. При производстве может меняться давление, температура и т.д.
Применение:
- переработка кормов;
- производство пластика и полиэтилена;
- изготовление труб;
- пищевое производство.
Немного истории
Схема экструдера для пластика.
Экструдер начали применять еще в далеком девятнадцатом столетии. А серийное производство этого оборудования началось в двадцатых годах прошлого века. Сейчас экструдеры значительно отличаются от тех, что были раньше.
В современной промышленности экструдеры пользуются большой популярностью, причем выбрать можно из самых разнообразных видов. Купить новый экструдер – достаточно дорогое удовольствие. Но есть экструдеры, которые можно сделать своими руками.
Наиболее простыми в изготовлении являются экструдеры для глины и кормовые. Чтобы самостоятельно сделать другие виды этого оборудования, необходимо иметь хотя бы какие-нибудь базовые инженерные знания. А для изготовления этих экструдеров требуется не так много времени, и материалы стоят недорого.
Вернуться к оглавлению
Детали экструдеров
Схема экструзии.
- Головка экструдера. Она состоит из корпуса, который обогревается, и инструмента формующего с отверстием. Корпус прикрепляется к экструдеру. Отверстие инструмента может быть сужающимся к центру или в виде круглого канала. Обязательно должен быть раздатчик в виде спирали.
- Корона или активатор улучшает адгезию поверхностей материалов. Активаторы бывают разные, они отличаются по мощности, ширине, бывают с фиксацией односторонней и двусторонней или же с изменяющейся шириной переработки поверхности.
- Горячий нож. Горячий нож достаточно просто устроен, но его нужно правильно направлять относительно рукава, которые движется. Данный элемент увеличивает выход продукции почти в два раза. Горячий нож используется в экономичных целях.
- Шнек может и отсутствовать в оборудовании. Он предназначен для того, чтобы была большая производительность и хорошая гомогенизация расплава обрабатываемого материала полимеров.
- Узел тиснения. Он нужен для придания пленке особой жесткости и товарного красивого вида.
- Узел, обеспечивающий вращение головки. Вращение головки экструдера размещает постоянные неровности пленки, при этом качество рулона делается лучше, но качество пленки не повышается.
- Фальцовочное устройство оборудования.
- Тянущее устройство экструдера.
- Намотчик оборудования.
- Обдувочное кольцо экструдера.
Вернуться к оглавлению
Экструдеры для глины своими руками
Для изготовления простейшего экструдера для глины потребуется обычная пластиковая бутылка любой формы.
Такие экструдеры называют экструдеры для лепки. С их помощью можно работать с разнообразными глинами и пластилином. Данные экструдеры позволяют делать различные детали и фигуры. К примеру, можно изготавливать человеческие волосы или отчетливо рисовать траву.
Основой для этого экструдера выступает простая пластиковая бутылка прозрачного цвета. Ее необходимо хорошо вымыть и высушить, и крышку тоже.
Из крышки с внутренней стороны нужно извлечь пластину. Сделать это можно иголкой или булавочкой. Далее в ней необходимо сделать отверстие, из которого будет выдавливаться глина. Его диаметр должен быть таким, как толщина желаемых линий. Это производится с помощью острого ножа. Края отверстия делаются гладенькими.
Дальше необходимо взять диск из металла, к которому нужно прикрепить ручку в форме буквы «Т». Получившийся экструдер должен быть похож на шприц. Пластина должна быть приготовлена из прочного материала, чтобы во время работы она не изменила свою форму под воздействием давления.
Вернуться к оглавлению
Немного об экструдере для сварки
Благодаря ручному сварочному экструдеру можно делать много видов разнообразных работ с полипропиленом и полиэтиленом.
Сначала может показаться, что данные материалы не являются очень распространенными и редко где применяются.
Но в действительности их применяют во многих сферах. Из подобных материалов с помощью данного типа ручного экструдера делают системы для очищения воды, различных типов емкости и т. д. Преимущественно данные материалы пойдут как вспомогательные, но без них в любом случае нельзя обойтись.
Сварочный ручной экструдер имеет ряд преимуществ. Любая выбранная модель экструдера для экструзионной сварки будет гораздо лучше других.
Главным преимуществом такого оборудования считается простота в эксплуатации.
Подобным экструдером работать можно абсолютно в любом помещении и при различных условиях. Проще говоря, для работы не надо подготавливать специально обустроенное пространство или рабочий цех.
Схема бесконтактной и контактно-экструзионной сварки.
Ручным экструдером для сварки можно делать швы на разнообразные формы и конструкции. Это достаточно удобно, ведь при этом можно самостоятельно контролировать всю работу. Нередко случается, что в одном районе шов нужно сделать тонким, а немного дальше – толще. Ни одно оборудование не может такого сделать автоматически.
Помимо всего вышеперечисленного, стоит учесть, что данное устройство не слишком дорого стоит. Его цена будет приемлема практически для любого человека. Экструдер сварочный необязательно применять во время производства. Довольно часто его применяют дома. Дальнейший уход и обслуживание не заберут много денег. Данный экструдер может производить свою работу в течение многих лет, и он всегда остается актуальным и нужным приспособлением.
Ручные сварочные экструдеры бывают таких видов:
- безшнековые;
- шнековые;
- комбинированные.
Комбинированные экструдеры уместно применять при обработке композитного товара. В данных устройствах применяют и дисковую зону, и шнековую часть. Данное оборудование еще называют червячно-дисковым. К тому же у данного типа экструдеров есть прекрасная смесительная особенность.
Экструдеры, которые не имеют шнеков, используют для производства раствора полимеров, имеющих элементы высоко качества.
Обычно, приобретая данную продукцию, в комплекте покупатель получает несколько специальных насадок и подставок, но производители разные, поэтому и комплектация оборудования также различная. Сварочный ручной экструдер может работать при температурах от 180 до 260°С. Чтобы привести в работу устройство, необходимо подключить его к электрической сети. Желательно подключать его к напряжению в 220 В.
Экструзионная сварка – достаточно сложный процесс, поэтому чтобы сделать своими руками экструдер, необходимо иметь определенные знания и навыки. Разумнее будет приобрести оборудование у надежного производителя.
Jinan Saibainuo Technology Development CO., LTD всегда придерживалась принципа качества жизни, развития за счет творчества, роста за счет кредита. В своей деятельности по производству и продажам мы получили широкую поддержку и высокие отзывы клиентов, а также хорошая репутация благодаря передовым технологиям, строгому менеджменту, отличному качеству и безупречному обслуживанию. Мобильный: 0086-18660789346 Электронная почта: [электронная почта защищена] Линия по производству кукурузных хлопьевВ качестве основного сырья для производства кукурузных хлопьев используется кукурузная мука, это очень хрустящая пища после экструдирования, гранулирования, шелушения, жарки и приправы.Его выдающейся характеристикой является обилие сложных углеводов и пищевых волокон, а также мы можем добавлять некоторые микроэлементы и минералы. Он очень популярен на рынке из-за высокой питательной ценности, вкусности и удобства.
Эта строка содержит следующую машину: Смеситель → Винтовой конвейер → Одношнековый экструдер → Воздушный конвейер → Машина для шелушения → Автоматическая фритюрница → Опрыскиватель сахара → Роликовый → Hoister → Духовой шкаф Линия по переработке кормов для домашних животных
Объединив опыт исследований и разработок пищевого экструдера с рынком, компания Saibainuo со временем разрабатывает многие типы линий по переработке кормов для домашних животных. Эта строка содержит следующую машину: Смеситель → Винтовой конвейер → Двухшнековый экструдер → Воздушный конвейер → Духовой шкаф → Распылитель масла → Роликовый → Конвейер охлаждения Контактное лицо: г-жа Дженнифер Юань |
Введение в экструзию нитей и экструдеры своими руками
33 В настоящее время одним из самых больших недостатков 3D-печати является относительно высокая стоимость филамента, т. е.е. 3D-принтер (термо-) пластик, расходные материалы для вашего 3D-принтера. Цены на 3D-принтеры постоянно падают, но цены на филаменты не идут по тому же пути. Мы договорились, что доступность филамента намного выше, чем 2 или 3 года назад, как и выбор цвета. Даже материалы для 3D-печати становятся все более разнообразными и доступными.
Но цены, особенно на нить хорошего качества, особо не упали. Хотя мы наблюдаем рост конкуренции между производителями промышленных нитей, что в долгосрочной перспективе должно привести к увеличению массового производства и общему снижению цен, цены на нити по-прежнему колеблются на уровне 22-30 долларов за 1 кг катушки.Вы даже платите до 50 долларов за 500 г специальной нити. Эти цены настолько высоки отчасти потому, что производство и продажа филаментов — очень прибыльный бизнес.
СКАЧАТЬ ПЕЧАТЬ ЭТОГО ПОЧТА В PDF-формате
Просто заполните эту форму, чтобы загрузить PDF-файл для печати этого сообщения и сохранить его навсегда!
Щелкните здесь, чтобы загрузить файл PDF.
Здесь вступают в игру домашние или настольные экструдеры для волокон. Некоторые хитрые изобретатели и изобретатели разработали способ, позволяющий частным лицам производить пластик для 3D-принтера в домашних условиях, всего за небольшую часть его розничной цены.Фактически, они разработали так называемый «экструдер нити » для домашнего использования, то есть машину, способную извергать пластиковую нить, которую вы впоследствии можете использовать в своем 3D-принтере. На фото ниже показано, как выглядит такой экструдер. На фото 1 изображена машина Noztek Pro, элегантный настольный экструдер из Великобритании. Давайте кратко рассмотрим принципы работы этих машин, прежде чем анализировать процесс производства филамента, а также цены на сырье.
Фото 1. Экструдер для волокон Noztek Pro
Принципы работы
На иллюстрации ниже представлен простой обзор общих принципов работы стандартного настольного экструдера для волокон.
Иллюстрация 2 — Основные части и принцип работы экструдера для филамента
Основная часть экструдера представляет собой цилиндр, содержащий шнек (также иногда называемый «шнеком» или «сверлом»), который соединен с нагревателем (или термокамерой, или нагревательным элементом) на своем дальнем конце. С другой стороны, шнек соединен с электродвигателем, который посредством механического воздействия перемещает так называемые гранулы смолы (см. Фото 9 ниже) через цилиндр к нагревателю. Пеллеты непрерывно подаются самотеком из бункера (своего рода питающей воронки).Поскольку двигатель непрерывно приводит в движение шнек, гранулы смолы проталкиваются в нагреватель. Гранулы термопласта размягчаются и плавятся из-за тепла, а затем механически проталкиваются через фильеру. При проталкивании мягкого термопласта через матрицу он образует непрерывную нить с диаметром матрицы. Этот процесс называется экструзией, отсюда и термин «экструдер». На фото 3 более подробно показаны некоторые из этих частей.
Фото 3 — Детали Notzek Pro
Но есть и отличия между экструдерами.Некоторые используют более крупные двигатели в сочетании с системой зубчатого привода, другие используют шаговые двигатели, непосредственно приводящие в движение шнек. Большинство типов экструдеров допускают замену матриц двух стандартных размеров для трехмерной нити: 1,75 мм или 3 мм. У некоторых есть механизм охлаждения с воздушным вентилятором, у других нет, а у некоторых даже есть система автоматической намотки, чтобы намотать экструдированный материал на катушку. Что касается электроники, некоторые из них позволяют очень детальную настройку температуры, другие — очень простые. Просто взгляните на фотографии ниже, на которых изображено множество различных типов экструдеров.Но будьте уверены, их основные принципы работы всегда одинаковы.
Фото 3 © Bender24601
http://www.thingiverse.com/thing:83570
Фото 4
© Бен Фишлер
Фотография 5 © Befu
http://www. soliforum.com/topic/4188/another-filament-extruder-design-and-build-with-machining/
Фото 6
© FilaFab
Фото 7
© Хью Лайман
Как видно из приведенных выше примеров, большинство имеющихся в продаже экструдеров для экструзии в домашних условиях представляют собой комплекты, которые должен собирать покупатель.Хотя приведенная выше иллюстрация 2 может дать вам некоторые идеи о том, как выглядят различные части, мы хотели бы дать нашим читателям реальный практический опыт. Поэтому мы будем использовать гладкий и готовый к работе экструдер от Noztek, чтобы идентифицировать большинство различных рабочих частей такой машины.
Фото 8 — Описание деталей экструдера Noztek Pro
© Noztek
После объяснения основных принципов работы экструдера, давайте теперь посмотрим на процесс экструзии филамента.
Процесс экструзии нити
Нить изготавливается из так называемых «гранул сырой смолы». Фотография № 9 дает вам хороший пример того, как выглядят эти гранулы. Обратите внимание, что гранулы на этой фотографии предназначены для литья под давлением и изготовлены из материалов, которые могут не подходить для 3D-печати — если вы хотите купить гранулы для экструдирования нити в домашних условиях, вам нужно искать гранулы, подходящие для экструзии, а не для литье под давлением.Если вы не уверены, какой тип гранул вы собираетесь приобрести, просто отправьте письмо производителю или оптовику, который может помочь вам в этом вопросе.
Фото 9 — Гранулы сырой смолы — Слева направо: акрил, АБС и стекловолоконный нейлон
© Ides.com
Окрашивание нити
Эти гранулы смолы (т.е.филаментное сырье) обычно белые или прозрачные и имеют размер всего несколько миллиметров. Они должны быть смешаны с так называемой «маточной смесью», которая представляет собой специальные гранулы, используемые для окрашивания пластмасс (так называемые «цветные маточные смеси») или для придания пластмассам других свойств (т. е.е. «маточная смесь добавок»). Цветные маточные смеси представляют собой концентрированные смеси цветных пигментов, инкапсулированных во время теплового процесса в смолу-носитель, которую охлаждают, а затем нарезают в гранулированную форму. Взгляните на Фото 10, чтобы понять, как выглядят такие цветные суперконцентраты.
Фото 10 — Примеры цветных суперконцентратов
© Wisegeek.org
Поскольку цветные маточные смеси содержат концентрированные цветные пигменты, вам нужно только добавить небольшое количество маточной смеси, чтобы придать цвет целому килограмму гранул необработанной смолы.На фото 11 показаны необработанные гранулы, смешанные с некоторыми гранулами маточной смеси, чтобы получить вишнево-красный цвет, тогда как на фотографии 12 показаны различные пропорции добавления гранул маточной смеси для получения более светлых или более насыщенных цветов.
Фото 11 — Сырые гранулы, смешанные со смесью вишнево-красной маточной смеси — полученный цвет показан на красной табличке с образцом © Ides. com
Фото 12 — Слева направо — соотношения красителей в маточной смеси 1%, 2% и 3%
© Ides.co
Итак, добавляя один определенный цвет маточной смеси к сырой смоле, можно создать нить этого определенного цвета.Но вы также можете создавать новые цвета, смешивая разные суперконцентраты цветов — чтобы точно знать, какой цвет вы получите, обязательно ознакомьтесь с рекомендациями производителей и введите в Google термины «смешивание цветов» или «таблица основных цветов». Мы также рекомендуем вам провести собственное исследование, записывая при этом используемые пропорции суперконцентратов и полученные результаты. После того, как вы нашли подходящие цвета или проверили, что хорошо сочетается, мы рекомендуем вам опубликовать эти результаты, поскольку в сети все еще очень мало информации о соотношениях и конкретных обзорах маточных смесей.Вы также можете написать нам письмо по адресу info [at] 3dprintingforbeginners.com, и мы опубликуем ваши выводы на нашем сайте.
Почему информация о пропорциях смешивания мастербатчей и общих рекомендациях по экструдированию все еще скудна в сети? Что ж, экструзия филамента в домашних условиях — довольно новая концепция, но со временем информация, скорее всего, умножится. Но мы определенно рекомендуем прочитать отличный блог Дэвида Смита под названием «Биты в атомы», особенно его статьи о смешивании и соотношении мастербатчей.[РЕДАКТИРОВАТЬ: похоже, что блог Дэвида Смита уже некоторое время не работает. Вы все еще можете найти соотношения мастербатчей на WayBackMachine здесь.] Посмотрите, каких крутых цветовых вариаций удалось достичь Дэвиду с его экструдером Filastruder, а также какие крутые объекты может создавать такая разноцветная нить.
Фото 13 — Разноцветная катушка
© Дэвид Смит
Фото 14 — Многоцветные печатные объекты
© Дэвид Смит
У вас также есть другие альтернативы экструдированию разноцветной нити, например раствор Ричарда Хорна, a.k.a. RichRap из http://richrap.blogspot.com придумал. Рич просто использует нейлон 618 вместе с цветами Tie-Dye, чтобы создать свою многоцветную катушку, но результат смешивания разных цветов в экструдере потенциально одинаков. Однако весь процесс Rich немного более громоздкий, и вам нужно будет получить довольно много материалов, чтобы получить эти потрясающие результаты. Более подробную информацию можно найти здесь: http://richrap.blogspot.co.uk/2013/04/3d-printing-with-nylon-618-filament-in.html.
Фото 15 — Многоцветная нить накала
© richrap.blogspot.com
Фото 16– Разноцветная нить накала
© richrap.blogspot.com
Процесс производства нити
Давайте кратко рассмотрим процесс производства филамента. Производители промышленных нитей обычно используют большие линии экструзии нитей, которые представляют собой большие промышленные машины, которые экструдируют несколько нитей за одну партию и с очень постоянным диаметром, но которые также способны выдавливать огромное количество нитей за час.Они нагревают очень большие количества сырых гранул вместе с заранее заданными красочными маточными смесями (для достижения консистенции цвета производители используют заранее определенные соотношения, определяемые их собственными исследованиями и разработками). Но суть производственного процесса для этих промышленных экструзионных линий почти такая же, как и для производственного процесса вашего экструдера в домашних условиях. Взгляните на иллюстрацию 17 ниже, где резюмируется основной производственный процесс. Обычно промышленные экструзионные линии больше похожи на фото 18 и 19.
Рисунок 17 — Упрощенный процесс экструзии нити
Фото 18 © http://www.fiordtrimmerline.com
Фото 19 © http://www.carrier-bags.com
Некоторые заметные различия заключаются в том, что ваша экструдированная нить DIY, вероятно, не охлаждается водой сразу после экструзии, что ваш домашний экструдер может выдавливать только одну нить филамента и, следовательно, может обеспечивать только относительно небольшое количество нити в час, в то время как промышленные линии могут экструдировать много сто килограммов в час.Кроме того, домашний экструдер может быть снабжен или не оснащен намоточным устройством для волокна, то есть устройством, которое автоматически наматывает экструдированное волокно на рулоны или катушки. Помимо контроля натяжения нити, некоторые намотчики также осуществляют автоматический контроль качества диаметра нити, так как неравномерное выдавливание нити приводит к изменению диаметра нити, что, в свою очередь, влияет на качество ваших отпечатков.
Стоимость экструзии нити
Но, наверное, самый главный вопрос: сколько стоит произвести килограмм самодельной нити? Начнем с того, что по понятным причинам вы не можете сравнивать стоимость экструзии в домашних условиях со стоимостью промышленного производства.Как и в любом промышленном процессе, экструзия волокна подчиняется правилам экономии за счет масштаба. Следовательно, чем больше промышленный производитель может закупить в больших количествах, тем больше у него будут снижаться цены на сырье. Эти правила не могут быть применены к очень небольшим количествам, купленным одним человеком, который хочет выдавить несколько катушек для личного использования.
Таким образом, цены, представленные ниже, являются ориентировочными, тем более что экструзия волокна частными лицами является довольно новой областью и почти не ведется розничных операций.Большинство компаний, продающих гранулы и суперконцентраты, являются оптовиками, и большинство из них работает с минимальными объемами заказов от 10-25 кг и более. Хотя недавно некоторые умные люди определили потенциальный рынок, который кажется развивающимся, и начали продавать сырье в меньших количествах. Поиск надежного поставщика, поставляющего качественный материал в розничных количествах и по приемлемым ценам, по-прежнему остается сложной задачей. Кстати, в настоящее время мы составляем список надежных поставщиков, занимающихся розничной продажей пеллет и суперконцентратов.Если вы заказали их и довольны материалами и их услугами, напишите нам по адресу info [at] 3dprintingforbeginners.com. Мы опубликуем этот список на нашем сайте.
На момент написания этой статьи (май 2014 г.) килограмм гранул необработанной смолы стоит от 3,5 до 4 евро. Цветные суперконцентраты стоят от 1,2 до 3,5 евро за килограмм и очень часто доступны только в больших количествах (5-10 кг и более). Помните, что это ориентировочные оптовые цены. Принимая во внимание цены и коэффициент электроэнергии, используемой для экструзии, цену машины, ее использование и амортизацию, а также различные мелочи, вы можете произвести свой килограмм нити примерно за 5-7 евро. Это колоссальная экономия 70% по сравнению с розничными ценами. Итак, если вы принимаете во внимание только стоимость филамента, возможно, стоит подумать о приобретении собственного экструдера для филамента. По общему признанию, вам нужно напечатать много, прежде чем вы сможете получить даже, поскольку экструдеры, доступные в настоящее время, не из дешевых. Если вы хотите приобрести экструдер, мы составили список имеющихся в продаже машин для экструзии в домашних условиях с указанием их цен. Взгляните на таблицу ниже.
Экструзия пластиковых нитей для отходов
Но помимо цены, очень интересная, часто упускаемая из виду и недооцененная часть наличия экструдера для нитей в домашних условиях заключается в том, что он эффективно может помочь замкнуть цикл пластиковых отходов.Ваш домашний экструдер позволяет не только перерабатывать и делать нить из определенных пластиков, но и эффективно повторно использовать их (после некоторой базовой обработки) в ваших отпечатках. В 2011 году мировое производство пластмасс составило около 280 миллионов тонн (источник: http://www.plasticseurope.org/information-centre/press-releases/press-releases-2012/first-estimates-suggest-around-4-increase -in-plastics-global-production-from-2010.aspx)! Хотя усилия по переработке постоянно улучшаются, пластик представляет собой огромную экологическую проблему (просто посмотрите на свалки или целые пластиковые острова, плавающие в море, угрожающие дикой природе и т. Д.), так как большая его часть выбрасывается после предполагаемого использования.
Свалка мусорных бутылок
© diverfunctionaldesigns.blogspot.com
Сборщик бутылок для мусора
© globalflare.com
Свалка бутылок для отходов
© Corbisimages
3D-печать в сочетании с экструзией пластика в домашних условиях может изменить это. Нет, мы не пишем, что переработка и 3D-печать этого пластика изменят мир, как утверждают некоторые. Но мы убеждены, что 3D-печать и экструзия пластиковых отходов могут повлиять на эту бесполезную систему отходов, как только более крупные массы поймут, что эти «отходы» можно с пользой повторно использовать для других целей. Возьмем, к примеру, знакомую большинству из нас бутылку: пластиковую бутылку для молока (если в вашем регионе нет пластиковых бутылок для молока, представьте себе бутылку с водой или бутылку шампуня). Большинство этих бутылок изготовлено из полиэтилена высокой плотности, то есть из полиэтилена высокой плотности. Они помечены цифрой 2 в соответствии с идентификационным кодом смолы, который представляет собой набор символов, размещенных на пластике, чтобы определить, из какого типа пластика изготовлен предмет.
Иллюстрация 19 — Идентификационные коды смолы
© www.gbpyrolysis.com
Обычно эти бутылки просто выбрасывают после использования. Если вы заботитесь об окружающей среде, вы действительно перерабатываете эти пластмассовые отходы. Но если у вас есть экструдер и 3D-принтер, вы должны сохранить бутылки, так как вы можете повторно использовать их для создания собственной нити. Итак, как утилизация пластиковых отходов работает на практике?
Убедившись, что на вашей бутылке есть маркировка HDPE (или PE-HD, или проштампована цифра 2), вы должны тщательно очистить ее, чтобы не осталось ни единого исходного содержимого. Также снимите наклейки, цены или отпечатки на бутылке. Затем вам нужно разрезать бутылку на мелкие кусочки, которые затем пропустите через своего рода измельчитель, измельчитель или аналогичную машину (например, DIY Mini Shredder Маркуса Тимарка), чтобы разрезать их на кусочки, которые могут поместиться в ваш экструдер. Весь процесс подготовки пластиковой бутылки для отходов показан на Рисунке 21 ниже.
Обычно куски должны иметь размер примерно 5 на 5 мм, чтобы шнек или сверло могли транспортировать измельченные куски в тепловую камеру экструдера.Постоянство размеров переработанных и измельченных пластиковых деталей помогает избежать отклонений диаметра экструдированной нити. Когда измельченные пластиковые кусочки станут достаточно мелкими, их можно будет загружать в бункер (коническая часть, используемая для подачи гранул в шнек / сверло) вашего экструдера. Хотя весь этот процесс подготовки может занять больше времени, чем простое использование гранул сырой смолы, самым большим преимуществом использования пластиковых отходов является стоимость.
Экструзия одного килограмма переработанной пластиковой нити из отходов оценивается примерно в 10 долларов центов [0.1 $, 0,07 евро, 0,05 фунта стерлингов], согласно доктору Джошуа Пирсу из Мичиганского университета. Эта очень дешевая нить накала представляет собой огромную экономию по сравнению с нитью для розничной продажи! И у вас есть дополнительное преимущество в том, что вы используете пластик, который обычно выбрасывали бы. Это определенно проливает новый свет на пластиковые отходы, которые теперь можно использовать для превращения во что-то полезное, вместо того, чтобы создавать неудобства и проблемы для окружающей среды. Потенциал этого развития был также определен основателями благотворительной организации под названием Ethical Filament Foundation.Недавно мы помогли его основателю выступить с основным докладом и очень скоро опубликуем более подробную статью об этом известном проекте.
Фото 20 — Измельчитель пластмасс от FilaMaker
© FilaMaker
Фото 21. Бутылка для молока очищена, нарезана и измельчена
© thingiverse.com
Чтобы понять огромный потенциал, стоящий за этим, просто посмотрите на Dremelfuge, напечатанный командой доктора Пирса (фото 22) с использованием пластика из использованных бутылок для молока. Дремлфуге (http: // www.thingiverse.com/thing:1483) сам по себе является невероятно полезным элементом и может использоваться в лабораториях в качестве ротора для центрифугирования стандартных микроцентрифужных пробирок (стандартные пробирки Eppendorf на 1,5 или 2 мл или аналогичные). Этот предмет для 3D-печати вместе с широко доступной дрелью / многофункциональным инструментом Dremel можно превратить в полупрофессиональную центрифугу (центрифуги необходимы для извлечения ДНК), что в противном случае стоило бы вам минимум 300-500 долларов! Особенно если учесть, что вы можете разогнать Dremel до 33000 об / мин на полной мощности, а это значит, что у вас в гараже может быть так называемая «ультрацентрифуга».
Это решение, с одной стороны, позволяет людям попробовать «самодельные биологические исследования» без необходимости вкладывать много денег в дорогостоящее оборудование, особенно если они просто хотят немного повозиться. С другой стороны, что еще более важно, в определенных регионах мира, где эти технологии еще недоступны по разным причинам (высокая стоимость, отсутствие инфраструктуры, технологические ограничения и т. Д.), Люди благодаря этим разработкам получают возможность проводить Исследование ДНК.Просто подумайте о возможностях, которые открываются в развивающихся странах, которые часто используют огромное количество пластиковых отходов.
Фото 22 — Дремлфуг, напечатанный из использованных бутылок из-под молока
© Джошуа Пирс
Поэтому перспективы повторного использования пластиковых отходов очень интересны, даже если мы все еще находимся в начале этого захватывающего развития. По общему признанию, экструзия пластмассовых отходов и их печать — дело еще не простое, и все еще требует самостоятельной работы и серьезной работы, т.е.е. процесс еще далек от совершенства. Например, печать HDPE на 3D-принтере может оказаться сложной задачей, поскольку вам понадобится подогреваемая кровать и даже может потребоваться тепловая камера на вашем 3D-принтере, чтобы избежать деформации.
Кроме того, важно знать, что пластик не может быть переработан и подвергнут повторной экструзии снова и снова, поскольку он становится хрупким и начинает проявлять структурные проблемы при повторном нагревании слишком много раз. Вам нужно будет следить за своим пластиком « тепловая история », так как каждый цикл нагрева дополнительно разрушает полимерные цепи, из которых состоят ваши термопластические материалы.Поэтому рекомендуется всегда смешивать новые гранулы или новый пластиковый измельченный материал со старыми смесями во время экструзии, чтобы сохранить прочность материала. Еще одна вещь, на которую следует обратить внимание, — это загрязняющие вещества, такие как пыль, грязь или различные материалы, которые не должны попасть на ваш отпечаток или ваш экструдер. Поэтому хороший экструдер всегда должен быть оснащен соплом, объединяющим так называемый «фильтр расплава », который похож на кусок очень тонкой проволочной сетки, за исключением тех загрязнений, которые могут попасть в вашу нить. Это позволяет избежать блокировки горячих концов принтера, которые могут стать дорогостоящими!
Наш пример повторного использования пластиковых отходов касается повторного использования пластиков HDPE. Однако для экструзии можно использовать и другие пригодные для повторного использования полимеры. Но здесь нужно быть очень осторожным, поскольку некоторые типы пластика, такие как ПВХ или другие полимеры на основе хлора, могут выделять опасные пары, которые могут серьезно угрожать здоровью. Если вы экспериментируете с экструзией пластиковых отходов, вам нужно знать, что вы делаете! Прочтите свой паспорт безопасности материала, если таковой имеется!
Список экструдеров
В настоящее время существует лишь несколько коммерческих настольных экструдеров, позволяющих экструдировать нить в домашних условиях.Для удобства читателя мы составили краткий список моделей, доступных в настоящее время, вместе с некоторыми из их наиболее важных характеристик.
Экструдер | Скорость экструзии | Напряжение | Сменные матрицы / фильтр расплава в комплекте | Комплект / в сборе | Цена |
---|---|---|---|---|---|
Noztek Pro | 1 кг / 3-4 часа | 110 В и 220 В | Да, в комплекте (1,75-3 мм) Фильтр в комплекте | В сборе | 843 € 695 £ 1164 $ |
FilaFab | Н / Д | 220 В | Да, но Н / Д, если имеется. N / A re filter | В собранном виде | 849 € 699 £ 1170 $ |
Filamaker | Н / Д | Н / Д | Н / Д Фильтр? | Комплект | 1200 € 984 £ 1655 $ |
FilaBot Original | 300 м / ч | 110 В и 220 В | Да, в комплекте Фильтр? | В собранном виде | 899 $ 652 € 534 £ |
FilaBot Wee Kit | 150 м / ч | 110 В и 220 В | Да, в комплекте Фильтр? | Комплект | 649 $ 470 € 386 £ |
Filastruder | 1 кг / 12 часов | 110 В и 220 В | Да, в комплекте (1,75–3 мм и без отверстий) Фильтр? | Комплект | 299 $ 217 € 178 £ |
Экструдер для волокон Lyman — Сделай сам | Н / Д | Н / Д | Н / Д Фильтр? | DYI | 499-900 $ 362-653 € 297- 535 £ |
Экструзионный бот | 120 м / ч | Н / Д | Н / Д Фильтр? | В собранном виде | 625 $ 453 € 372 £ |
Что касается скорости экструзии, производители указывают либо вес в час, либо количество метров в час. Для лучшего понимания, вы можете принять во внимание, что катушка 3 мм PLA на 1 кг содержит +/- 110 метров, а катушка 3 мм ABS на 1 кг содержит +/- 130 метров нити. Для катушек 1,75 мм следует считать +/- 330 метров для PLA и +/- 400 метров для ABS. Обратите внимание, что эти значения могут измениться в зависимости от плотности используемой вами нити.
Мы связались с разработчиками Noztek Pro, поскольку этот экструдер, по нашему мнению, представляет собой одну из самых многообещающих конструкций среди всех существующих коммерческих экструдеров, доступных сегодня.Он не только легко собирается, но и является одним из наименее дорогих экструдеров в своем классе. Тем не менее, у него есть все необходимые навороты: сменные матрицы, встроенный фильтр расплава, механизм охлаждения через встроенное вентиляционное отверстие и планетарный двигатель с высоким крутящим моментом. Согласно Noztek допуск на экструзию составляет около 0,04 мм. Что касается скорости экструзии, кажется, что Noztek может выдавить 1 кг за 3-4 часа. И в качестве особого подарка ребята из Noztek добавляют бесплатную упаковку гранул ABS по 500 г.
СКАЧАТЬ ПЕЧАТЬ ЭТОГО ПОЧТА В PDF-формате
Просто заполните эту форму, чтобы загрузить PDF-файл для печати этого сообщения и сохранить его навсегда!
Щелкните здесь, чтобы загрузить файл PDF. Обычно Noztek Pro можно использовать для экструзии ABS и PLA, но ребята из Noztek сказали нам, что экструзия HDPE также не представляет никаких проблем. Он не только имеет температуру плавления 180 ° C, но и производит высококачественную нить, а также дает возможность перерабатывать отходы бытового пластика и превращать их во что-то функциональное.В этом отношении цвета также хорошо сочетаются. Что касается паров, нам сказали, что фактические испарения не намного больше, чем испускаемые на 3D-принтере. Но Noztek рекомендует использовать экструдер в хорошо вентилируемом помещении. Экструдер не поставляется с измельчителем или намоткой нити. Последний продается отдельно на сайте Noztek за 295 фунтов стерлингов.
Ребята из Noztek пообещали нам тестовый образец, поэтому мы будем держать вас в курсе любых дальнейших разработок, так как мы опубликуем наши результаты на сайте.Так что проверяйте регулярно.
Экструдер | Еммак
1- Döner besleyicili ya da dikey karıştırıcı formunda tartımlı rezerve depo
2- Besleme helezonu
3- Kondüsyoner
4- Ekstrüder ’den oluşur.
Ekstrüzyon prosesi besleyici ürünleri pişirme, ekstrüde etme, genişletme, starilize etme, şekillendirme ve yapı kazandırmada hızlı ve ekonomik olarak kullanılır. Ekstrüzyon ile yağlı tohumlar içinde anti metobolitler zararsız hale getirilir ve hücreleri parçalanır.Hububatların içerisindeki nişasta kolay hazım edilebilir hale gelir. Bitkisel ve hayvansal yağları стабилизировать эдер. Bazı hayvansal ве bitkisel atıkları, yem katkı maddesi olarak yeniden kullanılır duruma gelir.
Islak Ekstrüzyon işlemi; kondüsyoner içerisinde buhar ile homojen olarak harmanlanmış yem; ekstrüder gövdesine yerleştirilmiş vida sistemi içinde iletilirken kesit daralması ve sürtünme ile basıncı arttılır, ayrıca bu esnada ısı da üretilir. İsteğe ве ürüne bağlı olarak dışarıdan ısı takviyesi de yapılabilir.Yüksek ısı ve basınc dahilinde pişirme ве suyun buharlaşması sağlanır. Бу işlem sonucunda işlenmiş hammadde genişleyip, şekil ve yapı kazanmış olup içerisindeki anti Metabitler zararsız hale getirilir. Örnek olarak soya tanesinde ve küspesinde TRIPSIN ignitörü bulunmaktadır. Бу-ингибитор протеинлерин çözünmesi ve amino asitlerin ayrışmasını sağlayan, pankreas enzimlerinden biri olan tripinenziminin etkisini önler. Benzer diğer igntörler gibi ısıya karşı duyarlı olup, etkisi pişirme ile yok edilebilmektedir.Ингибитор трипсина? Rünün yok edilmemesi durumunda; Proteinler ве амино asitlerden faydalanılamaz ve yemin verimliliği büyük oranda düşer, canlı büyümesinde gerileme gözlenir.
Kuru Ekstrüzyon İşlemi; бухар кулланилмадан, хелезон беслейчи тарафиндан öğütülmüş йем, вид системы ичинде илэтилиркен кесит даралмаси ве сюртюнмеси иле базынц арттилыр ве бу эснада исы да üretilir. Bu ısı yemin pişmesini sağlar. Kısa olan bu pişirme süresinde anti Metabitler zararsız hale getirilir, proteinlere zarar vermeden yağ hücrelerini parçalanır. Böylece yemdeki yağ ortaya çıkar. Serbest bırakılmış yalar ekstrüderi terk ettiği anda nihai ürüne sıvı görünümü verir. Örnek olarak soya fasulyesi ekstrüderden 145 ° C sıcaklıkta sıvı görünümünde çıkar. Birkaç saniye içinde ürün yağı Absorbe eder ve yağ soya unu içinde stable, yüksek miktarda ve sindirilebilir durumda kalır.
ÖZELLİKLER
- Canlı ağırlığında (kg bazında) artış
- Hijyenik yem
- Besin değeri artışı sağlanması ve sindirimin kolaylaştırılması
- Besleyiciliği ve büyümeyi engelleyen ignitörlerin önlenmesi (трипсин ингибитор, üreaz, липоксидаз vb.)
- ekillendirilebilirlik
- Контроллер edilebilir yoğunluk
- Raf ömründeki artış
- Atık yem miktarının en aza indirgenmesi
- Dayanıklı iç tasarım
- Modüler kovan tasarımı sayesinde kolay bakım
- Yedek parça ve müşteri servisi